台を製作し、テーンテーブルとモーター、直進フィーダー、カメラを仮設置しました。この後に配電盤を設置します。
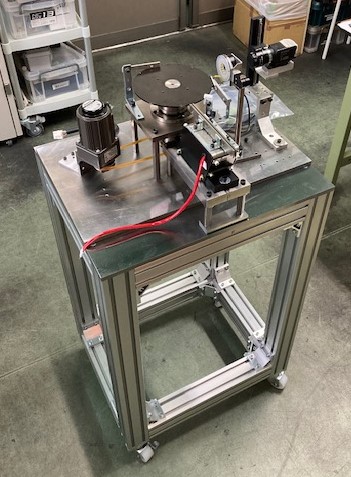
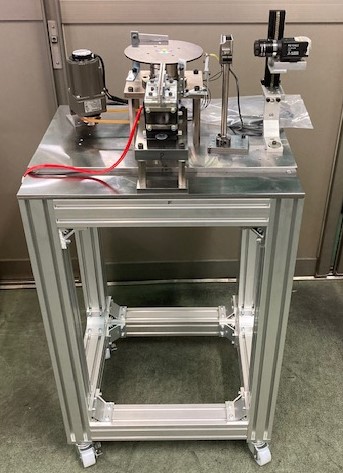
台を製作し、テーンテーブルとモーター、直進フィーダー、カメラを仮設置しました。この後に配電盤を設置します。
ミスミ殿のアルミフレームで台を製作します。直進フィーダーを設置する為、図太いアルミフレームを選定しています。移動が出来るようにキャスターも取り付けます
接着材を塗布する事が出来る装置(チュービングディスペンサー)を入手しました。どのような仕組みになっているかわからず使用するまで手間取りましたが、ホントに少量の接着剤の塗布が出来ました。エレシリンダと組合わせて何か新しい提案が出来そうです!
ターンテーブルに乗り込むブランクが揺れてしまうので、ストッパーを設けて揺れを防止します。画像センサのトリガタイミングを取る為のセンサーの設置を行いました。
お客様の依頼で、ねじ(M6長さ6)の頭部を旋盤で加工します。ねじ部をチャックして削りますが、強くチャックするとねじ山が潰れてしまうし、弱いと加工中にねじがぶっ飛んでしまいます。
チャックの加減で良いところを見つけるのに5コのねじをぶっ飛ばしてしまいました。また削るのに負荷を与えないよう切り込み量を少しで行なっていたので、かなりの時間がかかりました。
お客様からバリが発生する製品の選別が出来ないかの相談を受け、ターンテーブル式の検査機の提案を行いました。
どんなものなのか実際にわかる様にデモ機を製作します。
まずは円盤部分と直進フィーダーを組付けます。
お客様から相談を受けて提案している検査装置は、キーエンスさんの画像センサとレーザーセンサを使用します。 本当に検査判定が出来るのか、?であった為、実機でデモンストレーションを行って頂きました。どちらも問題ないことが確認出来ました。
キーエンス営業担当の〇〇さん、ありがとうございました。
製作した治具部をハンドプレスに取付て、完成しました。
この装置で切断したパイプの断面は丸形状を保っています。
樹脂パイプ(細いストロー状)を切断する装置を作ります。
ニッパーで切断出来ますが、切り口が潰れてしまいます。潰れないように切断出来ないかとの相談を受けて、装置の提案をし、製作依頼を受けました。
まずはハンドプレス機に載せる治具部の製作をしました。
検査業務を行っていただいている担当者に、検査ブランクを受ける箱を作業台より低い位置で設置したいとの意見を受け、作業机に引き出しを追加する検討を行いました。しかし机下のスペースの確保が難し事がわかった為、ひとまわり小さく低い机を設置する提案をし、あまり部材で製作してみました。作業がし易くなったとの意見を頂きました。